- WHAT IS STONE-TECH®?
- WHERE CAN STONE-TECH® BE USED?
- WHY DO YOU USE STONE-TECH®?
- HOW TO USE STONE-TECH®?
- TYPES OF STONE-TECH® AVAILABLE
- PACKAGING & STORAGE
- TIPS ON HOW TO USE STONE-TECH®
- HOW TO PREVENT BLOWOUT SHOOTS?
- SAFETY PREVENTION
- MSDS
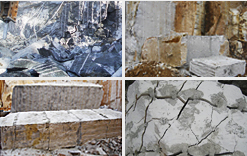
Product
![]() |
![]() |
![]() |
|
Demolition of object with regular shape
|
Demolition of object with irregular shape
|
Cutting
|
|
![]() |
![]() |
![]() |
|
Digging of tunnel
|
Vertical controlled demolition
|
Horizontal controlled demolition
|
|
![]() |
![]() |
||
Undergrand excavation
|
Trench excavation
|
The distance between two holes varies depending on the type of material to be cracked or cut. Diameter of hole is crucial to the cracking results. Too small holes are not in favor of good performance of the agent, while too big holes may cause blowout shoots. And the closer place of holes, the quicker to crack the object.
The following figures are only for reference. For the best possible use and to obtain best results, it is advisable to carry out experiment with STONE-TECH® before starting work.
Materials to be cracked/demolished |
Holes design |
||
Diameter(mm) |
Distance between two holes |
Depth |
|
Soft stone quarrying |
28-38 |
200-350 mm |
100% H |
Hard stone quarrying |
30-38 |
200-300 mm |
100% H |
Stone cutting / demolition |
28-40 |
200-400 mm |
90% H |
Plain concrete demolition |
30-40 |
300-500 mm |
80% H |
Reinforced concrete demolition |
32- 40 |
150-300 mm |
95% H |